views
Warehouse cooling is an integral part of managing logistics operations, inventory control, and product protection. With increasing demands for efficient storage, particularly in industries dealing with perishable goods, sensitive electronics, or chemicals, cooling systems are no longer a luxury—they are a necessity. In this detailed guide, we'll explore the best practices, technologies, and systems involved in warehouse cooling, focusing on how these solutions can enhance operational efficiency, reduce energy consumption, and maintain product integrity.
Why Is Warehouse Cooling Essential?
Key Benefits:
-
Product Preservation: Certain products, especially perishable goods like food and pharmaceuticals, require precise temperature control to avoid spoilage.
-
Improved Operational Efficiency: A well-cooled warehouse ensures optimal working conditions for employees, boosting productivity.
-
Compliance with Industry Standards: Many industries, such as food storage, require regulated temperature conditions for legal compliance and safety.
-
Energy Efficiency: Modern cooling technologies help minimize energy costs by reducing waste and optimizing system performance.
Types of Warehouse Cooling Systems
Choosing the right cooling system depends on factors such as warehouse size, product type, and regional climate. Here are the most common types of warehouse cooling systems:
1. Centralized Cooling Systems
A centralized system features a single cooling unit responsible for conditioning air for the entire warehouse. These systems are efficient for large operations where maintaining a uniform temperature across the facility is crucial.
-
Advantages:
-
Cost-effective for large-scale warehouses.
-
Consistent cooling across all storage areas.
-
-
Considerations:
-
High initial installation cost.
-
Maintenance requires specialized knowledge.
-
2. Evaporative Cooling Systems
Evaporative coolers are a popular choice for warehouses in dry climates. They work by using water evaporation to cool air, creating a comfortable environment at a lower cost compared to traditional air conditioners.
-
Advantages:
-
Energy-efficient and low operating costs.
-
Environmentally friendly.
-
-
Considerations:
-
Less effective in humid climates.
-
Requires regular maintenance to prevent mineral buildup.
-
3. Split Cooling Systems
These systems are split between an interior air handler and an exterior condenser unit. Split systems are ideal for medium-sized warehouses where zoning is important to maintain various temperature ranges.
-
Advantages:
-
Provides flexibility in temperature zones.
-
Lower installation cost than centralized systems.
-
-
Considerations:
-
Limited cooling capacity for large warehouses.
-
May require more frequent maintenance.
-
4. In-Rack Cooling Systems
In-rack cooling involves placing cooling equipment directly within the storage racks, which provides focused cooling where it's most needed. This method is excellent for high-density storage areas and ensures temperature consistency.
-
Advantages:
-
Precise control over temperature.
-
Efficient for storing sensitive items.
-
-
Considerations:
-
Higher upfront costs.
-
Suitable only for specific warehouse designs.
-
Factors to Consider When Choosing a Warehouse Cooling System
When selecting the right cooling system for your warehouse, it's important to consider the following factors:
1. Warehouse Size
The size of your warehouse directly impacts the type of system you choose. Smaller facilities may benefit from decentralized or split systems, while larger warehouses may require centralized systems for more efficient cooling.
2. Product Requirements
Consider the type of products being stored. Perishable goods like meat, dairy, or pharmaceuticals require constant temperature control, while electronics might need a specific humidity level to avoid damage.
3. Energy Efficiency
With rising energy costs, it's essential to choose a system that minimizes electricity consumption. Look for cooling solutions that offer high energy efficiency, such as evaporative or in-rack cooling, which use less energy compared to traditional air conditioning systems.
4. Climate and Location
The local climate plays a huge role in determining the most appropriate cooling system. For instance, evaporative cooling systems are best suited for dry climates, while refrigerated air systems are necessary in more humid or extremely hot areas.
5. Budget
While advanced cooling systems provide excellent performance, they often come with higher upfront costs. Assess your budget and consider the long-term savings offered by energy-efficient solutions when making your decision.
How to Optimize Warehouse Cooling for Maximum Efficiency
Once you have selected the ideal cooling system, here are some strategies to ensure it operates at peak performance:
1. Regular Maintenance
Maintaining your cooling system ensures it runs smoothly and efficiently. Regular maintenance tasks include:
-
Cleaning filters and evaporators.
-
Checking refrigerant levels.
-
Inspecting the system for leaks or damage.
-
Replacing worn-out parts before they fail.
2. Temperature Monitoring
Installing temperature sensors throughout the warehouse allows for real-time monitoring and control. This ensures that temperatures are kept within optimal ranges and prevents product spoilage.
3. Proper Insulation
Warehouse insulation is essential for reducing heat ingress and minimizing the load on cooling systems. Good insulation prevents cooling systems from overworking and reduces energy consumption.
4. Energy Management Systems (EMS)
Implementing an EMS helps monitor and control the energy usage of the cooling system. EMS can automatically adjust temperatures based on the time of day, occupancy, or product requirements to reduce energy waste.
5. Automated Temperature Control
Automated systems provide a more efficient way to maintain a consistent temperature by adjusting cooling capacity in response to real-time data, reducing energy consumption when demand is low.
Key Metrics to Track for Warehouse Cooling Efficiency
To ensure the cooling system remains cost-effective and operationally efficient, monitor these important metrics:
Metric | Description |
---|---|
Temperature Fluctuations | Measures variations in warehouse temperature to ensure stability. |
Energy Consumption | Tracks how much energy is being used to maintain the cooling system. |
Cooling System Downtime | Monitors the uptime vs. downtime of the cooling system to prevent interruptions. |
Maintenance Costs | Tracks the expenses related to system maintenance to determine ROI. |
FAQs About Warehouse Cooling
Q: How do I know if my warehouse needs cooling?
A: If you store products sensitive to temperature changes (e.g., food, pharmaceuticals, or electronics), a cooling system is essential to maintain product integrity and comply with industry regulations.
Q: What is the most energy-efficient cooling system for a warehouse?
A: Evaporative cooling systems are highly energy-efficient, especially in dry climates. For large warehouses, in-rack cooling systems can also offer energy savings by cooling specific areas instead of the entire space.
Q: How often should a warehouse cooling system be serviced?
A: Regular maintenance is essential to keep your cooling system functioning efficiently. It’s recommended to have your system checked at least twice a year or more frequently if it's heavily used.
Q: Can I install a cooling system in an already operational warehouse?
A: Yes, cooling systems can be retrofitted into existing warehouses. Depending on the layout and design, certain systems, such as split or in-rack cooling, may be more suitable for an upgrade.
Q: Are there cooling systems for smaller warehouses?
A: Yes, smaller warehouses can benefit from split cooling systems or decentralized solutions that are cost-effective and suitable for lower square footage.
Key Takeaways
Warehouse cooling is a critical factor in ensuring product safety, maintaining efficient operations, and controlling costs. With the right system in place, you can improve operational efficiency, reduce energy consumption, and comply with industry standards. By choosing the correct cooling system, implementing maintenance schedules, and optimizing energy usage, your warehouse can stay productive and cost-effective year-round.
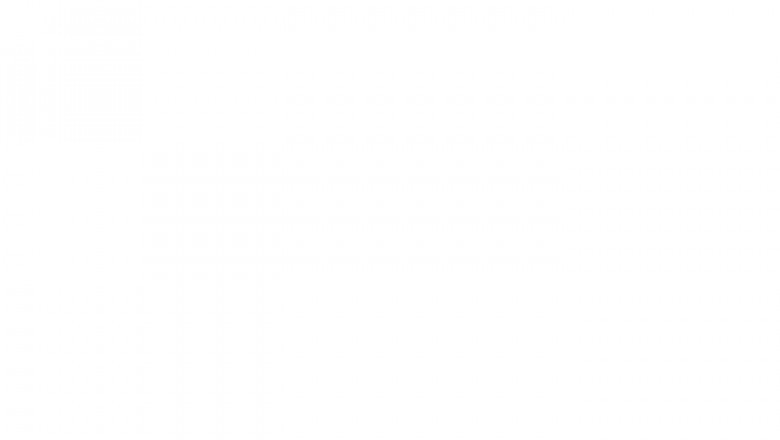

Comments
0 comment